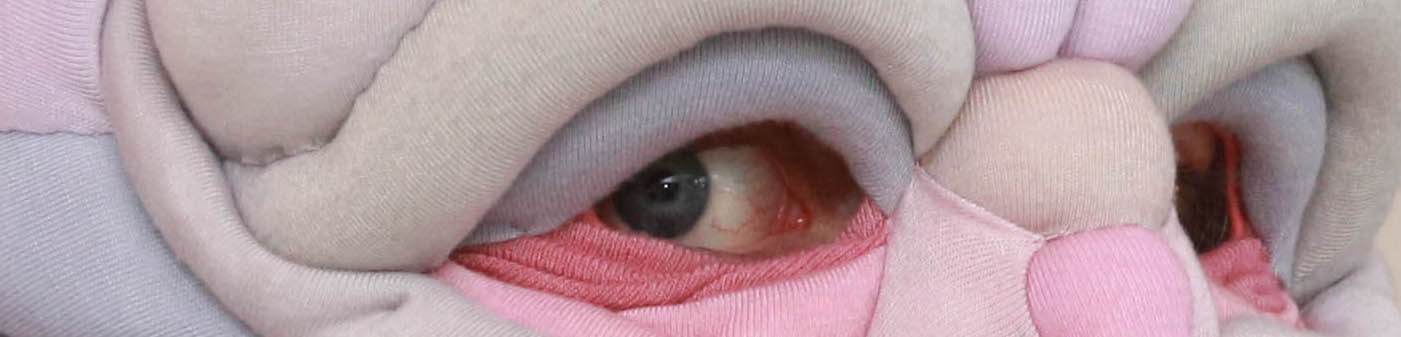
Squishies – amazing textile art
From Daisy Collingridge
Gloria and I have known Daisy Collingridge for a while now and there’s no doubt she’s an amazing artist in so many ways. I’m not using the word “amazing” lightly and you’ll see what I mean when you see her textile art, her “squishies”, in this article. Daisy was so nice to agree to answer some of my questions about her textile art and I’ve recorded her answers below.
What do you call these amazing creations that look like “fat suits”?
Daisy – “I affectionately refer to them as my ‘Squishies’. I spend so long making them that they definitely become animated characters to me. If asked to describe them I would say they sit in an awkward space between sculpture and performance art.”
Where and when did you get the inspiration for this?
Daisy – “I made the first ‘Squishy’ in 2016. It’s been a development process since then. Each time refining the technique as well as experimenting with colour palettes, weight, and pattern cutting. The inspiration is a hard one to decipher. My degree is in fashion design. The course was a conceptually led rather focused purely on making clothes. It gave me grounding in technical garment construction combined with freedom of thinking. My graduate collection was entirely free machine quilted. The ‘Squishies’ developed by pushing the technique of quilting to the extreme. Using layers of wadding sandwiched between fabrics to create extreme ‘puffs’- a pattern in relief. My work is always technique/craft led, rather than concept led, but it is unsurprising that I have chosen the human figure to explore. I come from a family of doctors, nurses and scientists. I loved biology and PE at school. The human body is fascinating: its ability to heal, to be pushed to physical limits and also to self-destruct. We are all made of the same components, yet as individuals we are all unique.”
How long does it take you to make one?
Daisy – “I’ve never timed it but I suggest they take a very long time to make. I did make Burt in 6 weeks, but I did nothing else but make Burt. They are predominately hand stitched which obviously takes a long time!”
What materials do you use?
Daisy – “Hand dyed jersey and cotton, wadding, weighted pellets, beanbag beans, thread, and sand.”
Is there any special skill you needed to learn?
Daisy – “Not really. Essentially the technique is hand-sewn appliquéd quilting. It is a bit like ‘Trapunto’ combined with crazy patchwork. Other techniques I use are pattern cutting to make the free hanging pockets as well as hand dying to get the tonal colour palettes.”
Do you have a clear vision of a piece before you start making it?
Daisy – “Ultimately I make on impulse with only a rough plan. I had a ‘How to make a teddy bear’ book as a child. In the book it suggested you should make the head first so that the bear could watch you make it the rest of its body. I have adopted this method. After I’ve dyed the fabric, I make the head first. I let the head inform me what the character will be. At this stage I may do a sketch of the ‘silhouette’ of the rough body shape and then plough on regardless.”
What people worldwide have been interested in you work?
Daisy – “My favourite story is that I made a dress for Bjork. It wasn’t one of my ‘Squishies’; it was a yellow quilted dress. That is still my biggest claim to fame.”
What do people want them for? How are they going to use and/or display them?
Daisy – “This is a question people ask me frequently. I wonder if people ask the same question of a painting or a sculpture? I accept they live in an awkward boundary between art, performance art, fashion and the dreaded ‘textile art’ tag. If they weren’t wearable and just existed as sculpture would they be accepted as sculpture? For me they are sculptures of the human form. They exist as objects of beauty and a point of reflection. They are no different than the men carved from stone at the British museum… except maybe their longevity.
Four ‘Squishies’ will be on show this Autumn; Burt, Clive, Dave and Hillary will be shown as part of the galleries at the Knitting and Stitching show (see www.theknittingandstitchingshow.com) this autumn in London, Dublin and Harrogate. They will be shown in still sculptural form. Though we might bring one to life.”
Do you have items for sale now?
Daisy – “Nigella is small version of the larger wearables. She is being shown at 108 Fine art in Harrogate in November (see 108fineart.com). She will be on sale there. I would like to use all four of them to create some imagery and film before I think about giving them new homes!”
Is this still a passion of yours, or are you on to something new?
Daisy – “Making 3D sculptures is definitely a passion. Its what I get most excited about. I think it is time to go back to an experimental phase. I’ve got so many things I want to play with and explore but it’s always hard to allow yourself the time to just play without necessarily producing something at the end.”
I, for one, hope that Daisy gives herself time to “just play”. I doubt very much that such activity of hers will produce nothing and I’m sure we’ll see some more new and amazing things from her in the future.
So it’s with great thanks extended to Daisy for sharing her experience with and passion for 3D sculptures and her “Squishies”. They certainly are amazing. And this isn’t the only example of amazing art that emanates from Daisy Collingridge, but that’s another story…
You can find out more about Daisy Collingridge using the following links;